Finishing
Finishing is an important step in fabrication and is usually the final step in preparing metal products prior to installation
Finishing enhances the corrosion resistance and durability of products, while also improving their appearance.
The type of finishing process used depends on the material of the fabricated part and can increase its resistance to chemicals, tarnishing and electrical conductivity.
By altering the surface of a fabricated part, finishing can make it easier to bond with and more durable over time.
Galvanising is the process of applying a protective zinc coating to steel to prevent rusting. The zinc acts as a barrier, preventing oxygen and water from reaching the steel and providing better corrosion protection. At SDR Fabrications, we use hot-dip galvanising, which involves immersing steel sections in a vat of molten zinc.
While galvanised steel will eventually rust, it will be protected for a much longer time than non-galvanised steel and will require less upkeep. Hot-dip galvanising provides both external and internal protection within hollow sections, and provides good abrasion and corrosion resistance. You can identify hot-dip galvanised steel by the crystallised pattern on its surface.
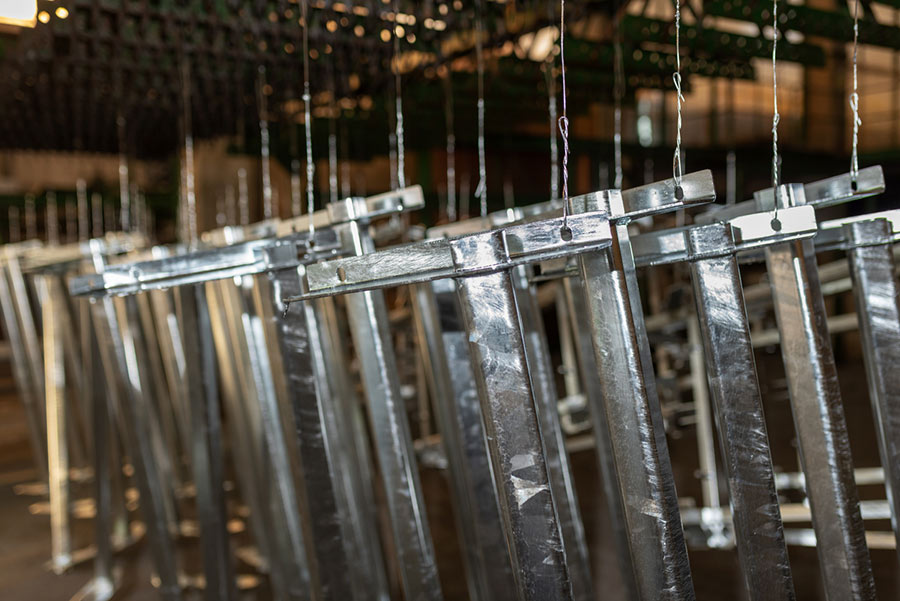
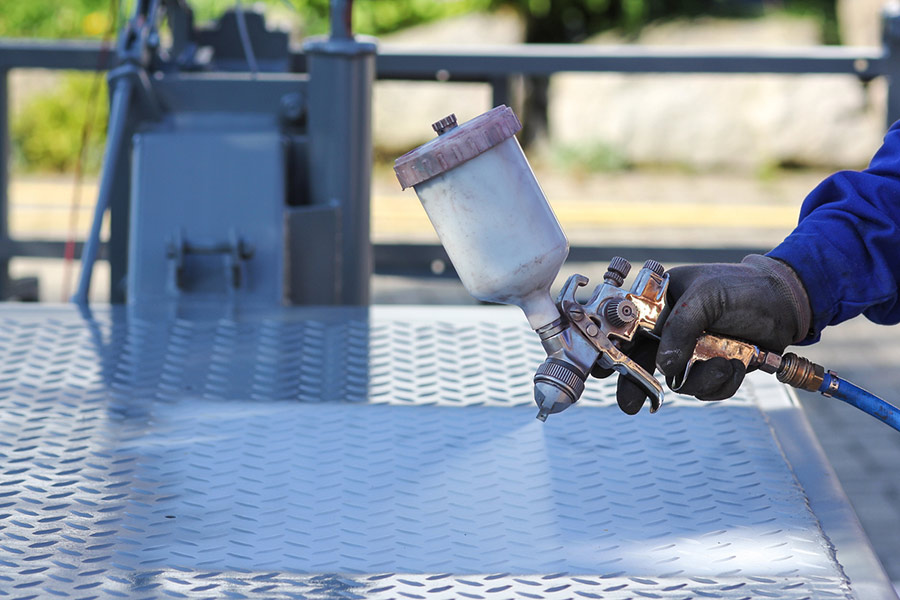
Polishing and Buffing:
Polishing and buffing are part of our finishing process where we use satene based polishing mops to remove imperfections such as scratches and lines. We then move on to finer abrasive pads until we achieve the desired finish. We can also provide a mirror finish upon request.
We also offer painting services to meet your desired RAL color. To ensure the best results, all surfaces are first prepared to receive a primer coat before the top coat is applied.
THINGS TO CONSIDER
Things to consider before deciding on your finish
- Which process suits the product end use?
- Does the finishing process provide the fabrication speed required?
- Is the finishing process cost effective?
- Is the finishing process suitable for the materials used?